ZeroAvia is working with a variety of OEMs and airlines to commercialize hydrogen powertrains or aircraft. Photo Credit: ZeroAvia, compilation by CW
Landscape image at top: ZeroAvia is working with Textron Aviation to certify the ZA600 hydrogen powertrain for retrofit of Cessna Grand Caravan aircraft.
ZeroAvia (Hollister, Calif., U.S. and Kemble, U.K.) is developing zero- emission powertrains that repower existing airframes, using electric motors, fuel cells and hydrogen (H2). Launched in 2018, the company has achieved a series of demonstrations, partnerships and industry investments that bring it closer to its goal of launching H2-fueled aircraft by 2025.
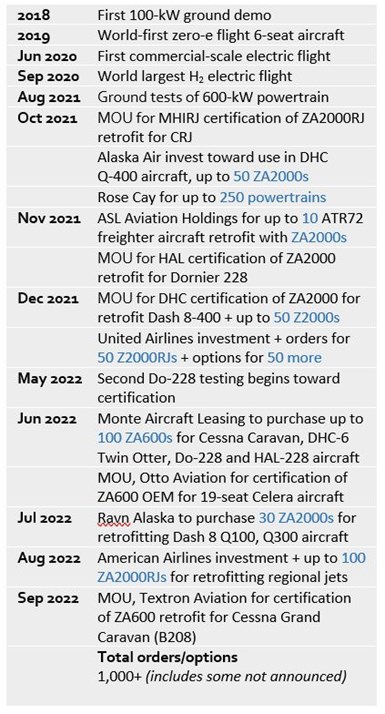
Photo Credit: CW
These partnerships include memoranda of understanding (MOU) with multiple aircraft OEMs to assist with achieving certification for aircraft using its retrofit powertrains. ZeroAvia also has agreements with OEMs, airlines and aircraft lessors for options to purchase powertrains, plus outright purchase orders once final demonstrations and certifications are complete.
ZeroAvia plans to launch its first commercial product — the 600-kilowatt ZA600 powertrain — in 2025, designed to retrofit aircraft with up to 19 seats and enable flights up to 300 nautical miles/480 kilometers. Its next launch will be the modular 2- to 5-megawatt ZA2000 in 2027, able to retrofit aircraft with up to 80 seats for flights up to 700 miles/1,100 kilometers.
ZeroAvia is also working with Mitsubishi Heavy Industries (MHI, Tokyo, Japan) and RJ Aviation Group (MHIRJ, Boisbriand, QC, Canada) to achieve certification of an even higher powered ZA2000RJ for retrofit of regional jets by 2030. MHIRJ acquired Bombardier’s (Montreal, QC, Canada) CRJ Series regional jet program in June 2020 including maintenance, engineering and support for more than 2,000 aircraft built since 1991. ZeroAvia plans to eventually add H2 powerplants for even larger aircraft, targeting five product families by 2040.
CGH2 to LH2 and composite tanks
“For the initial launch of the powertrain supporting smaller, up to 19-seat utility aircraft in 2025, we intend to stay with compressed gas [CGH2],” says Val Miftakhov, founder and CEO of ZeroAvia. “And then for another three to four years beyond that, we will use CGH2 in composite cylinders. We’re also looking at a number of conformable tank technologies from multiple manufacturers that are based on composites.”
“However,” Miftakhov continues, “we think larger aircraft, and eventually all aircraft, will move to cryogenic LH2. Our first application of LH2 will be for the 40-80-seat regional turboprops like the DeHaviland of Canada Dash 8 and ATR families with customers like Alaska Airlines in 2027. We see the most promising approach is using composite tanks and we are working with a couple of partners on that already. We want to see H2 aircraft flying as far as jet fuel aircraft, possibly in 10-20 years, and I think cryogenic tanks using lightweight composites will be key to that.”
We want to see H2 aircraft flying as far as jet fuel aircraft, possibly in 10-20 years, and I think cryogenic tanks using lightweight composites will be key to that.”
Miftakhov notes that composites are already being used for cryogenic propellant storage in space launch vehicles. “We’re hoping to help spur further development of that technology for aviation,” he adds. “Composites offer quite a bit of promise in terms of low mass and maximum hydrogen content inside the cryogenic tanks. We think composite dewars and similar technologies will result in systems with higher chemical energy — that is specific energy per unit of mass of the fuel system — compared to jet fuel.”
Hydrogen has a specific energy (120 MJ/kg) that is 2.8 times higher than traditional jet fuel (43 MJ/kg). However, its energy/volume is very low. This is why LH2 is so important for longer range flights, offering 40% more fuel storage than CGH2 in 700-bar Type IV composite tanks. “And that’s the first prerequisite to getting hydrogen aviation to the same or higher utility versus jet fuel-based aviation — getting enough chemical energy in the aircraft tanks so that we’re able to cross oceans. I think cryogenic tanks using composites will be key to achieving this, not for tomorrow, but possibly in 10 to 15 years.”
Certification and 50,000 cycles
Initial test results look promising, says Miftakhov, “but I think it will be challenging to develop a composite dewar that can be certified to aviation standards, including the G loads they will have to withstand. And we’ll need to certify these tanks with repeated loads, meaning the high flight cycles typical for smaller aircraft.” He notes a typical regional aircraft may experience 50,000 takeoff and landing cycles over its 20- to 30-year life, “and that’s a lot of cycles.” These cycles also entail emptying and refilling these tanks with cryogenic LH2, resulting in thermal cycling, which is another challenge.
“Initially, our plans are to deploy removable and replaceable tanks which can be in place for as many fueling cycles as possible, because we don’t expect, five years from now, for the industry to have a 50,000-cycle composite dewar for us to use,” says Miftakhov. “We’re designing some initial applications, probably for the end of the decade, with LH2 tanks that can be swapped in and out when needed. This can’t be done every cycle due to potential for damage and inspection requirements, so we need tanks that can be in place for as many cycles as possible. Eventually, I think we’ll need to match the capability of the existing jet fuel tank technology, which is again, roughly 50,000 cycles.”
Economics and supply chain
How large is this market? ZeroAvia currently has more than 1,000 provisional orders for ZA600 and ZA2000 powertrains. Just for a back of the envelope calculation, assuming two to four Type IV 700-bar CGH2 tanks per ZA600 powertrain would equal 700 to 1400 CFRP cylinders needed initially, perhaps from 2025 to 2028. The ZA2000 and ZA2000RJ powertrains will launch in 2027 and 2028, respectively, but will use LH2 and those tanks are still in development.
“This is a higher margin market versus automotive,” says Miftakhov. “We see it as similar to the market for fuel cells. For typical light-duty automotive vehicles using a standard internal combustion engine [ICE], the cost of power delivered is about $30 per kilowatt. For typical aviation turbine engines, it’s closer to $800-1,000 per kilowatt, ranging from small turbines to large ones. So, you have an order of magnitude price differential for aviation, which makes it easier to have a profitable fuel cell company, for example. We think there’s going to be a similar dynamic for composite LH2 tanks, with margins and pricing that will hopefully drive the supply.”
ZeroAvia has retrofitted its second Dornier 228 aircraft with a hydrogen powertrain for testing and certification. Photo Credit: ZeroAvia
According to the Clean Aviation Joint Undertaking — established to achieve climate-neutral aviation with zero emissions by 2050 — three-quarters of the global commercial fleet will have to be replaced to deliver the required emissions reduction to stay below 1.5°C in temperature rise. In fact, it proposes that next-generation aircraft need to enter service by 2035. “Rolling out such aircraft in 2045 or later simply won’t achieve what is necessary,” says Axel Krein, executive director of the Clean Aviation Joint Undertaking.
“I think 75% is a pretty aggressive number,” says Miftakhov. “Of course, it would be great to see that transformation across the entire fleet. But for composite hydrogen tanks, I think the actual number by 2050 is going to be lower than that. A good aggressive estimate, I think, is something between 30% and 50% of the fleet by 2050.”
Call for more partners
ZeroAvia is looking for more partners to help advance composites for both CGH2 and LH2 tanks. “We want to test different solutions,” says Miftakhov, “and we have the test vehicles.” The company received its second Dornier 228 aircraft in May 2022 and spent the summer retrofitting it with a more powerful ZA600 powertrain than previously tested. According to a September 2 article by Jon Excell in The Engineer UK, testing on that aircraft was getting ready to begin.
“We have test platforms, both for ground testing and flight testing, where we want to test various technologies,” says Miftakhov. “We’re already working with three or four companies on CGH2 and cryogenic LH2 tanks, and we’re looking for more qualified partners. So, if they have validated technology to contribute, tell your audience to give us a call.”
Related Content
SuCoHS project: Advancing composite solutions for parts with high thermal and mechanical loads
New materials, structural concepts and manufacturing using sensors for composites that resist fire, temperature and loads while providing weight and cost savings versus metals.
Read MoreJEC World 2023 highlights: Innovative prepregs, bio-resins, automation, business development
CW’s Jeff Sloan checks in with JEC innovations from Solvay, A&P, Nikkiso, Voith, Hexcel, KraussMaffei, FILL, Web Industries, Sicomin, Bakelite Synthetics, Westlake Epoxy and Reliance Industries.
Read MoreHigh-performance, high-detail continuous 3D-printed carbon fiber parts
Since 2014, Mantis Composites has built its customer and R&D capabilities specifically toward design, printing and postprocessing of highly engineered aerospace and defense parts.
Read MoreFord Mustang Dark Horse features Carbon Revolution carbon fiber wheels
The 19-inch, five-spoke Dark Horse wheels feature signature blue carbon fiber detailing, keeping with the blue accents throughout the vehicle’s interior and exterior.
Read MoreRead Next
Demonstrating composite LH2 tanks for commercial aircraft
Toray Advanced Composites and NLR discuss the Netherlands consortium and its 4-year project to build demonstrator liquid hydrogen tanks, focusing on thermoset and thermoplastic composites.
Read MoreZeroAvia partners with Otto Aviation to deliver new airframe design with hydrogen-electric option
ZeroAvia will optimize the fuel cell-powered electric propulsion systems for Otto’s transcontinental Celera aircraft design, reducing maintenance costs while increasing range.
Read MoreComposites end markets: Energy (2024)
Composites are used widely in oil/gas, wind and other renewable energy applications. Despite market challenges, growth potential and innovation for composites continue.
Read More